Automated Picking Workflow Gets the Right Items Found Fast
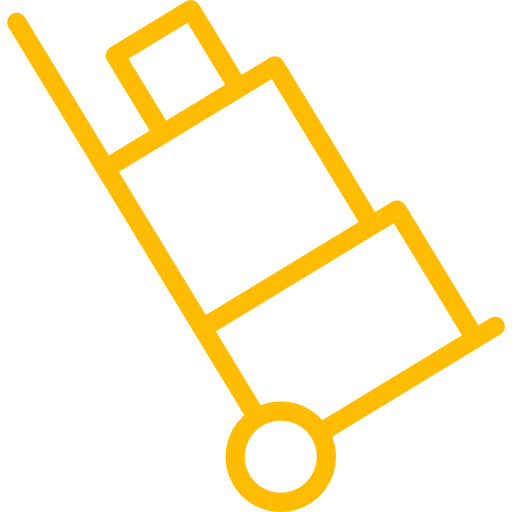
Warehouse Management software with workflow automation for picking help warehouse staff gather items for fulfillment as efficiently as possible.
When Warehouse Management software is integrated with a Business Management System or ERP or ecommerce website, the submission of a sales order to the BMS, ERP, or website can be automatically communicated to the software. The software in turn generates pick lists and wave-picking lists that tell warehouse staff which items need to be gathered from the warehouse.
An integrated Warehouse Management software can automatically define what needs to be picked, when it needs to be picked, and where to pick it from.
The lists also dictate not just the items to be picked but the order in which to pick them, sequenced and prioritized according to criteria defined by the business. User-defined Order Picking Priority aligns picking with other deadlines, workflows, and logistics such as production time, back order status, preferred customers, freight carrier arrivals, in-hands dates, and other criteria defined by the business. These automatically generated and prioritized pick lists effectively define a picking workflow optimized for real-world deadlines and logistics.
Warehouse Management software can also automatically generate wave-picking workflows. Wave-picking divides picking duties into groups, or waves, centered on common criteria. The business can use Warehouse Management software to define its criteria for wave creation.
For example, a wave might include all of the items needed from a particular physical location in the warehouse. The goal would be to reduce picking time by focusing picking operations on one limited physical area at a time. Waves might also be based on arrival times for certain freight carriers. If a new carrier arrives every two hours, for example, waves can be aligned so that orders are fulfilled in a sequence that corresponds with each carrier’s arrival.
Once it’s defined which items need to be picked in which order and wave, it becomes a matter of actually finding the product in the warehouse. Warehouse Management software with a built-in warehouse stock locator makes that easy. It can automatically attach zone, row, shelf, bin, and other location information to pick lists for optimal picking paths.
Simply based on the submission of sales orders, an integrated Warehouse Management software can automatically define what needs to be picked, when it needs to be picked, and where to pick it from. Warehouse Management software automatically generates optimized picking workflows.
Next: Automated Packing>>
Warehouse Management Home